Efficiency Boost through Cleanliness
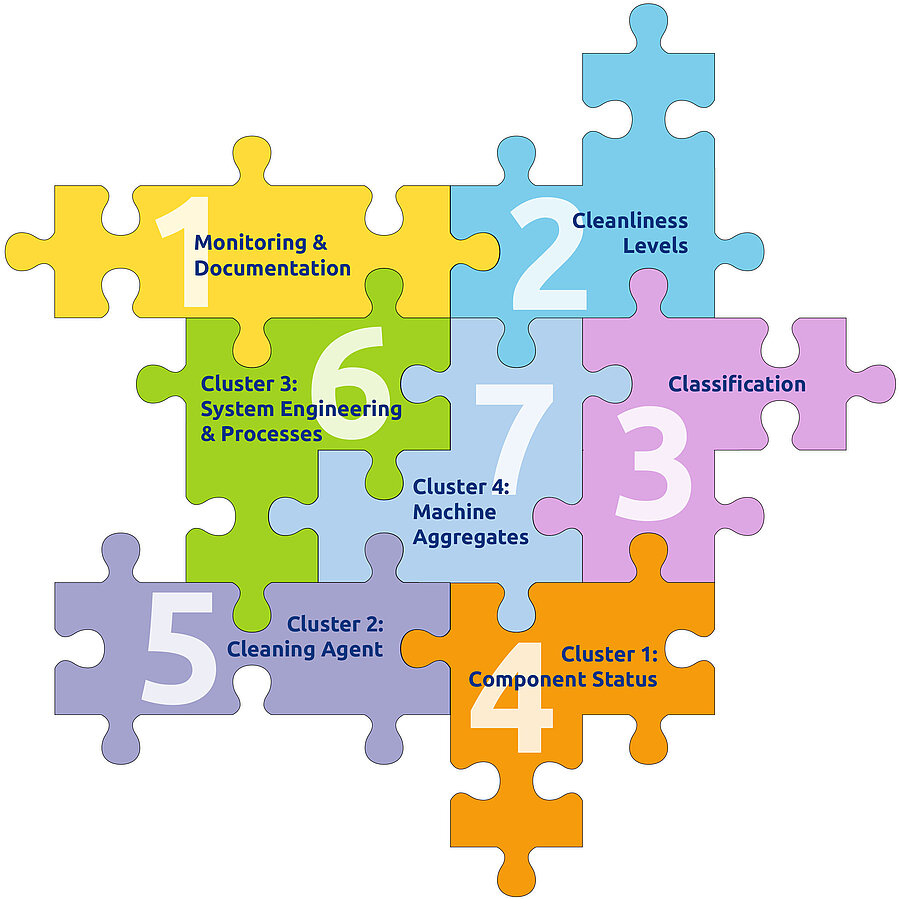
Economical and safely clean – with a System
Systems and processes for water-based parts cleaning are very flexible thanks to various control factors such as water, temperature, cleaning agent and mechanics, and efficiently meet even complex requirements. If parameters relevant to production and cleanliness change, they offer a wide range of optimization options. In view of this diversity, a structured approach is required to tackle the right points, and production managers should follow a fixed search grid.
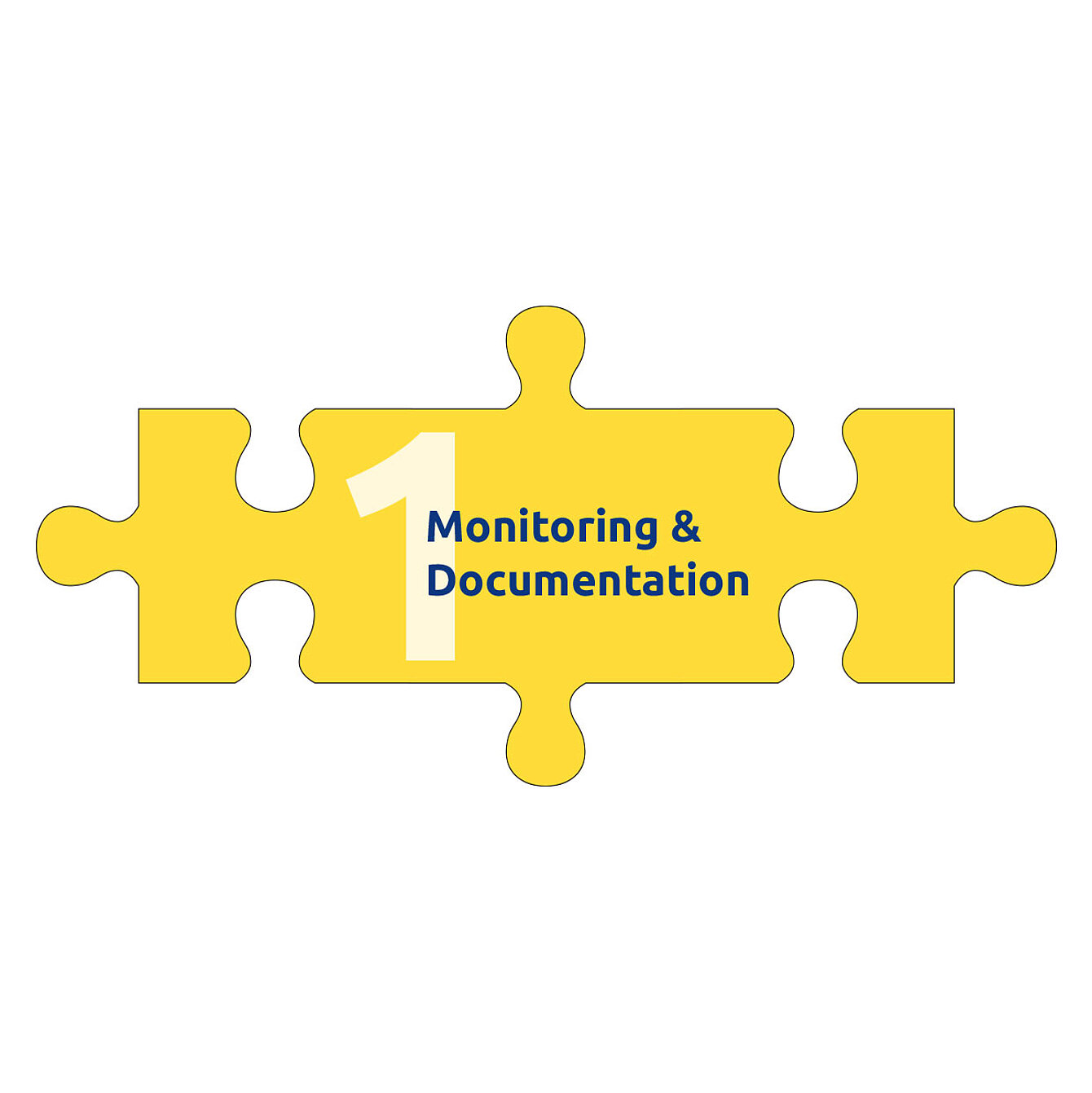
1 | Observation and Documentation: Identifying Potential
The definition of the required cleanliness is also essential for process design. If you follow the principle of “as clean as necessary”, you are on the right track. If the requirements change or the result is not as desired despite all care taken in the process design, the cleanliness should be redefined. It is crucial that all departments have access to the same concept of cleanliness. This requires a clear description of the problem and the objectives. If the cleanliness levels are defined across the board, optimization can be carried out on this reliable basis.
2 | Requirements Matrix and Analysis: Defining and correcting Cleanliness Levels
The definition of the required cleanliness is also essential for process design. If you follow the principle of “as clean as necessary”, you are on the right track. If the requirements change or the result is not as desired despite all care taken in the process design, the cleanliness should be redefined. It is crucial that all departments have access to the same concept of cleanliness. This requires a clear description of the problem and the objectives. If the cleanliness levels are defined across the board, optimization can be carried out on this reliable basis.
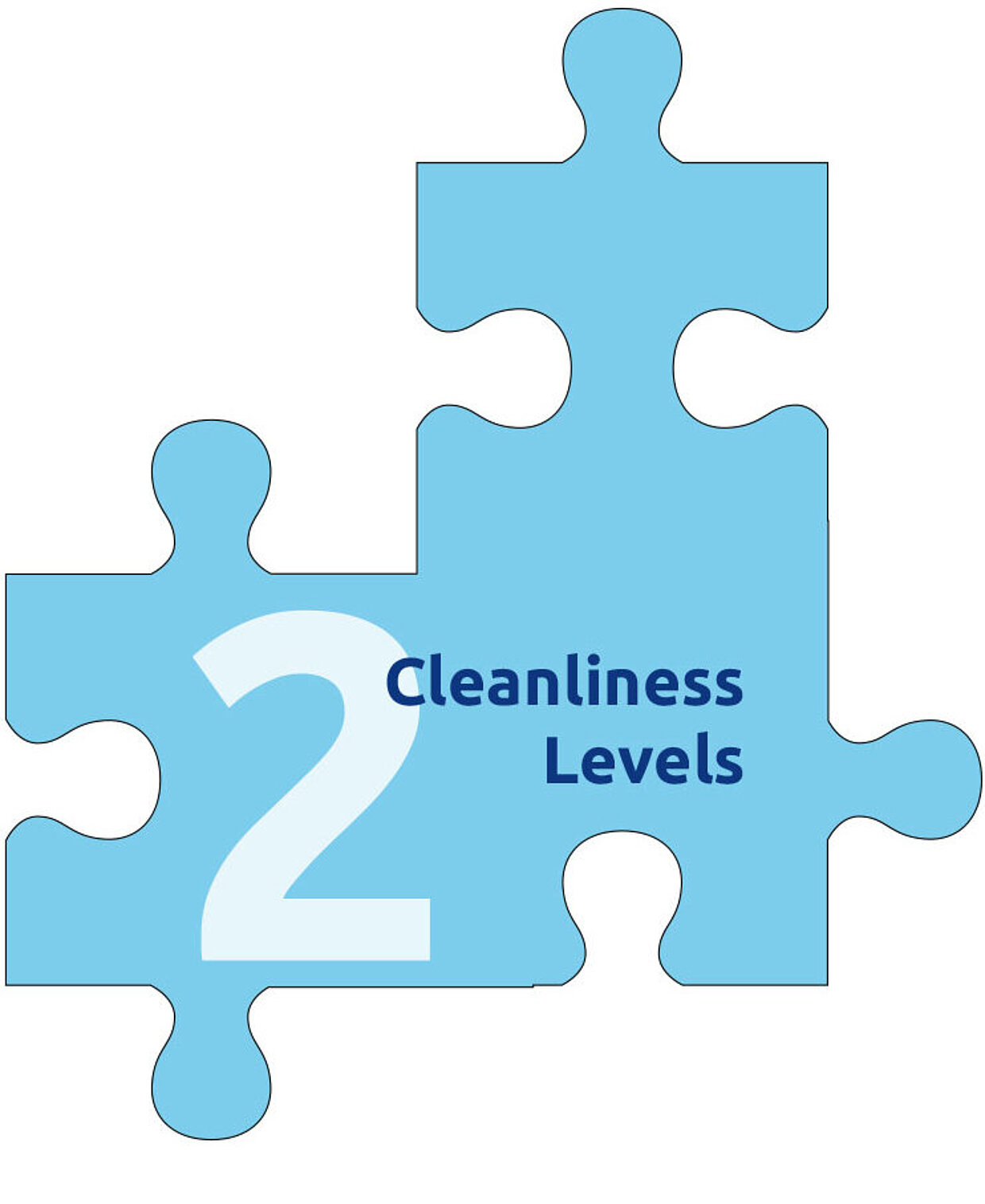
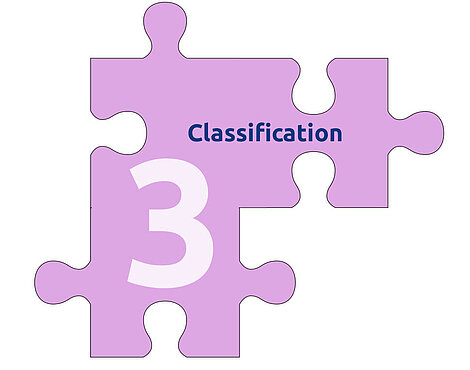
3 | Classification: Organizing the search Grid
Since aqueous cleaning is a highly variable system with a multitude of opportunities for the best process, the search for optimization options should be carried out in clusters along the following influencing variables: Parts, contamination, cleaning agent, temperature, system technology and process technology. These clusters should also be considered in terms of their interactions.
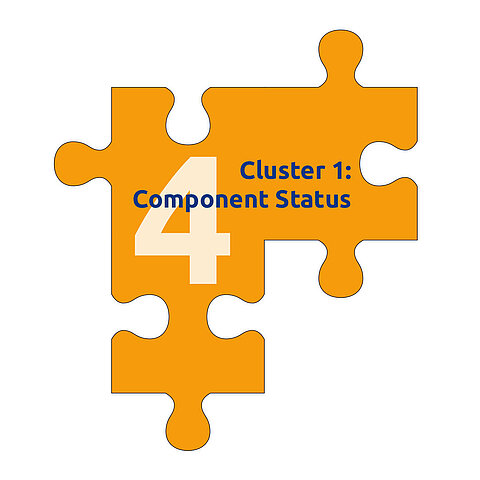
4 | Cluster 1: Component, Material and Contamination
These three parameters determine the cleaning process and play a central role in readjustment. Changes in the part spectrum, in the geometry, in the material, in the type and degree of contamination: all this must be analyzed in detail. Depending on the answer, the analysis chain is broken down further. If the result for film contamination no longer fits, adjustments to the temperature, cleaning agent or rinse water quality may be necessary. Are the results for particle contamination unsatisfactory, are chips and burrs not completely removed from the process? Then it is worth taking a critical look at the rinsing process and the "hardware". Maybe it is time to change the filter or to re-clean the cleaning chamber. Or the workpieces have to be placed differently in the basket to avoid spray shadows and recontamination by already loosened particles.
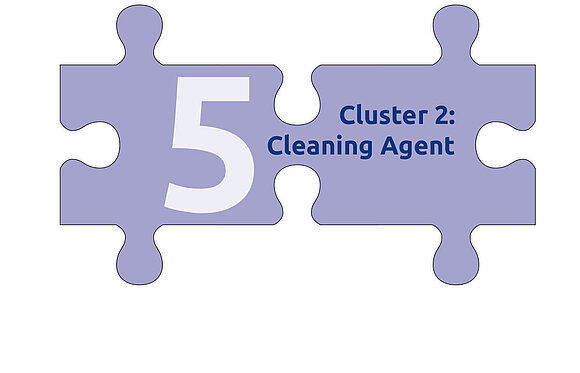
5 | Cluster 2: Cleaning Agent and Concentration
Poor cleaning performance requires an examination of the cleaning agents' field of action. Does the composition still match the soiling, according to the principle „like dissolves like“? It is possible that the concentration and composition no longer match, which requires adjustment or redosing. The temperature of the cleaning agent is also a factor: Is the process heat sufficient? Can the same result be achieved with less energy? In some cases, it is more efficient to work with less energy and a higher cycle time.
It is also important to observe the recommended bath life of the cleaning medium. A bath maintenance system provides security by monitoring the cleaning bath and adding more if necessary. This extends the service life and reduces costs as well as water and energy consumption. The process can be further optimized by retrofitting a powerful pump or a spray set. In the case of increased contamination or smaller components, larger media tanks with a cascaded design ensure greater cleaning reliability.
6 | Cluster 3: System Engineering and Processes
Further levers for troubleshooting or optimizing the entire process are system design, technology and process sequence. For example, the performance of the cleaning agent can be significantly improved by combining mechanical processes such as spraying, flooding or spray flooding and adjusting the temperature and time. A targeted sequence of these phases allows turbulence to be precisely controlled and optimized for the application. Adjustments can be made via nozzle position, nozzle pressure, additional movement of the spraying system and basket or the cycle time. Ultrasonic technology supports this interaction and, with the appropriate frequency, intensity and duration, can remove even stubborn soiling faster, more gently and with less energy input. The drying phase also offers potential for optimization by adjusting the temperature, interval and time.
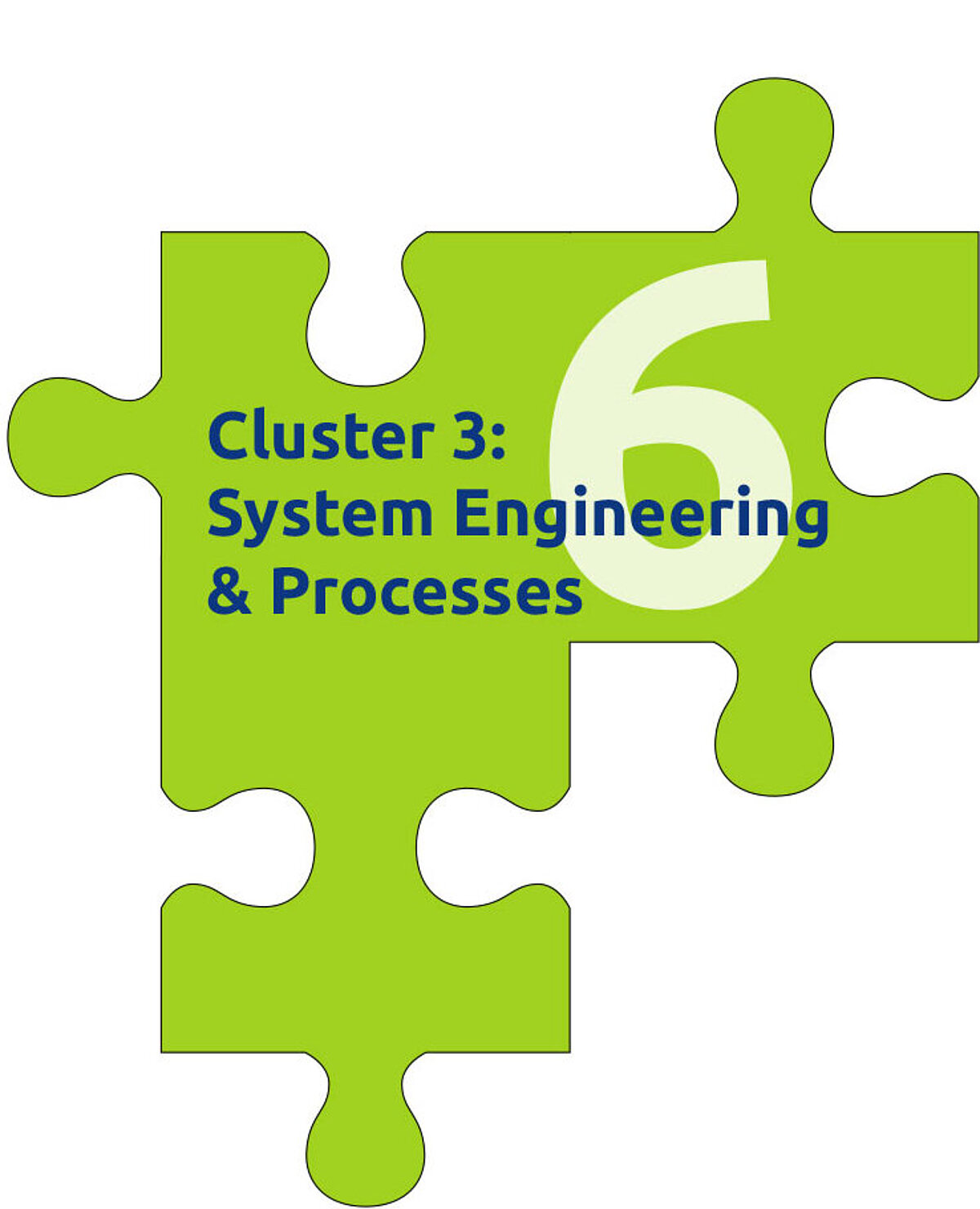
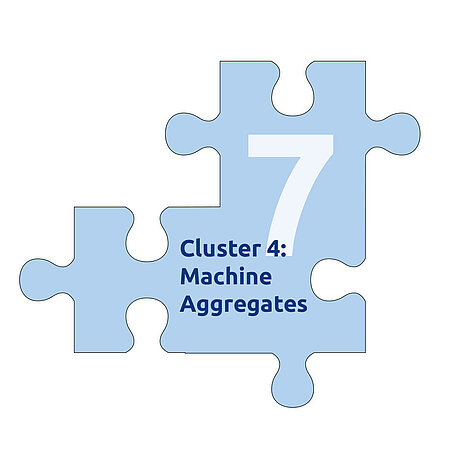
7 | Cluster 4: Machine Aggregates
The fourth strand of the analysis chain is the machine units. Wearing parts such as pumps, filters and sensors should be checked regularly and, if necessary, replaced with the latest standards in order to avoid performance deficits and conserve resources. Special attention should be paid to the oil separator as the dirtiest unit. If the separated grease builds up, the oil discharge is not sufficient, and maintenance must be carried out at shorter intervals. Further elements for greater machine efficiency are the insulation of media tanks, machine housings and units, as well as the optimized routing of air and water flows or the integration of heat exchangers.
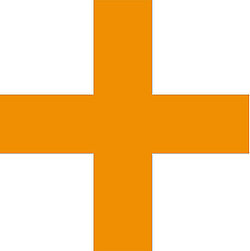
Building up know-how – with the Expertise of the Machine Manufacturer
Optimization is most effective when cleaning problems are identified early on, and their causes are correctly assigned. However, the necessary routine and systematic approach is often lacking. Especially in the case of overlapping error patterns, the wrong conclusions are drawn. This is also due to the fact that cleaning knowledge in companies is mostly based on experience, as no corresponding qualification can be acquired during vocational training or studies. All the more important it is to work on cleaning deficiencies methodically and to document even small changes precisely. Continuous further training builds up the necessary know-how and makes it safe for employees to apply.
The application engineers of the machine manufacturer play a central role here. They contribute their expertise in maintenance, consulting and training. They provide basic information or can take over project management for specific malfunctions and systematically guide the troubleshooting process. It is also important to involve the relevant specialist departments such as quality management, design, production and sales. They must be provided with the necessary information. This also requires the willingness to break new ground and build up internal capacities.
Close cooperation with partners such as MAFAC makes a decisive contribution to understanding parts cleaning as a quality assurance step, to always being on the cutting edge of technology and to upgrading in good time. For the consistet optimal cleaning performance.
Author:
Thomas Gutmann
Head of MAFAC Customer Support